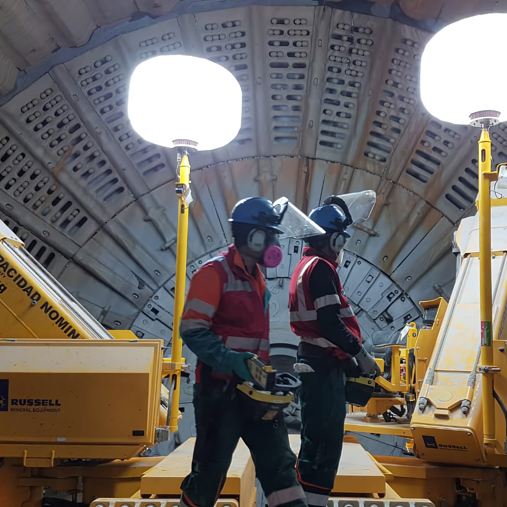
RUSSELL LINER EXCHANGE MACHINES
The trusted choice for mill operators globally. Our expanded, higher-performing range – from <400 kg to 10 tonne capacities – ensures fast, reliable, safe mill relining is available to every mine site.
Trust RME to raise the standard
As RME attains 40 years of pioneering progress and service to the global comminution industry, we continue to raise the standard of mill relining safety and productivity. Fast, reliable, safe, our comprehensive solutions are built-to-last, delivering higher mill availability and lower lifecycle cost. #WeAreRME.
Trust RME to raise the standard
RME’s expanded, future-proofed, field-upgradable RUSSELL Liner Exchange Machine range ensures fast, reliable, safe relining is even more accessible to every mine site. Our industry-leading technologies include roboticised, mechanised and mill liner handler solutions from <400kg up to 13 tonne capacities. Trusted and relied upon by mill operators and reline crews at 440 mine sites globally.
Trust RME to raise the standard
The RME Advanced Technology Mill Relining System™ is here. This groundbreaking product suite removes reline crews from hazardous zones inside and around the mill during liner exchange. Experience faster relining speeds with roboticised technology, and greater mill availability. Proven and commercially deployed—the future is now.
Trust RME to raise the standard
Explore the masterful RUSSELL Claw and RME BOLTBOSS™, part of the RME INSIDEOUT® Technology family, eliminating personnel from hazardous zones inside the mill during liner exchange. Compatible with all liner types and designed for RUSSELL Mill Relining Machines.
Trust RME to raise the standard
Reach higher, work safer, knock-in faster with THUNDERBOLT® – the industry's reliable, trusted and comprehensive worn liner removal system. THUNDERBOLT® Recoilless Hammers from 250 to 2000 Joules ⋅ Jibs and monorail suspension ⋅ THUNDERBOLT Elevating Platforms™ ⋅ THUNDERBOLT SKYPORT™ ⋅ THUNDERBOLT SKYWAY®
RME is the world's trusted Original Equipment Manufacturer (OEM) of fast, reliable, safe grinding mill relining technologies, asset support and optimisation services.
Mill relining is the most specialised and important task in the maintenance of a mineral concentrator. Mill relining dictates shut down times, mill availability, throughput, and therefore, mine site profitability.
RME’s driving passion has always been to eliminate fatal risk and visibly, defensibly, and sustainably improve our Customer’s concentrator performance.
Since our beginnings in 1985, the RME Mill Relining System – a comprehensive suite of products for every step on the mill relining path – has significantly reduced our Customers’ relining times and created safer working environments.
Looking ahead, RME remains dedicated to maximising the performance potential of the RME Mill Relining System for every Customer – past, present and future.
Discover today how the RME Mill Relining System is delivering exceptional safety and performance for our Customers around the world.
The trusted choice for mill operators globally. Our expanded, higher-performing range – from <400 kg to 10 tonne capacities – ensures fast, reliable, safe mill relining is available to every mine site.
Since 1997, THUNDERBOLTs have revolutionised liner bolt removal time and safety. See the wider range and their new faster, safer semi-automated capabilities.
Ensure mill relining equipment safety, productivity and longevity with RME's regionally-based inspections and servicing, critical spares provisioning and certified training.
Since the introduction of the RME Mill Relining System, we’ve quartered our Customers' traditional mill relining times. In addition, a great many safety issues associated with manual relining activities have been eliminated.
This same pursuit has driven our development of RME's Advanced Technology suite which removes the need for crew to be inside the mill during relining – an environment which enables us to significantly accelerate machine movements and relining speeds.
For almost 40 years, we’ve worked with hundreds of mine sites globally to optimise their mineral processing operations. Our mission is to work with you to create shorter shutdowns, higher mill availability and safer working environments.
RUSSELL MRMs manufactured since 1985
RUSSELL MRMs still in service and supported RME
THUNDERBOLT Recoilless Hammers manufactured since 1990
Mine sites / Countries with RME assets
International Sales and Service Centres
Employees worldwide