THUNDERBOLT ORBIT
The THUNDERBOLT ORBIT™ is a literal revolution for cone crusher head nut change outs and the fastest, safest method for removal and tensioning by far.
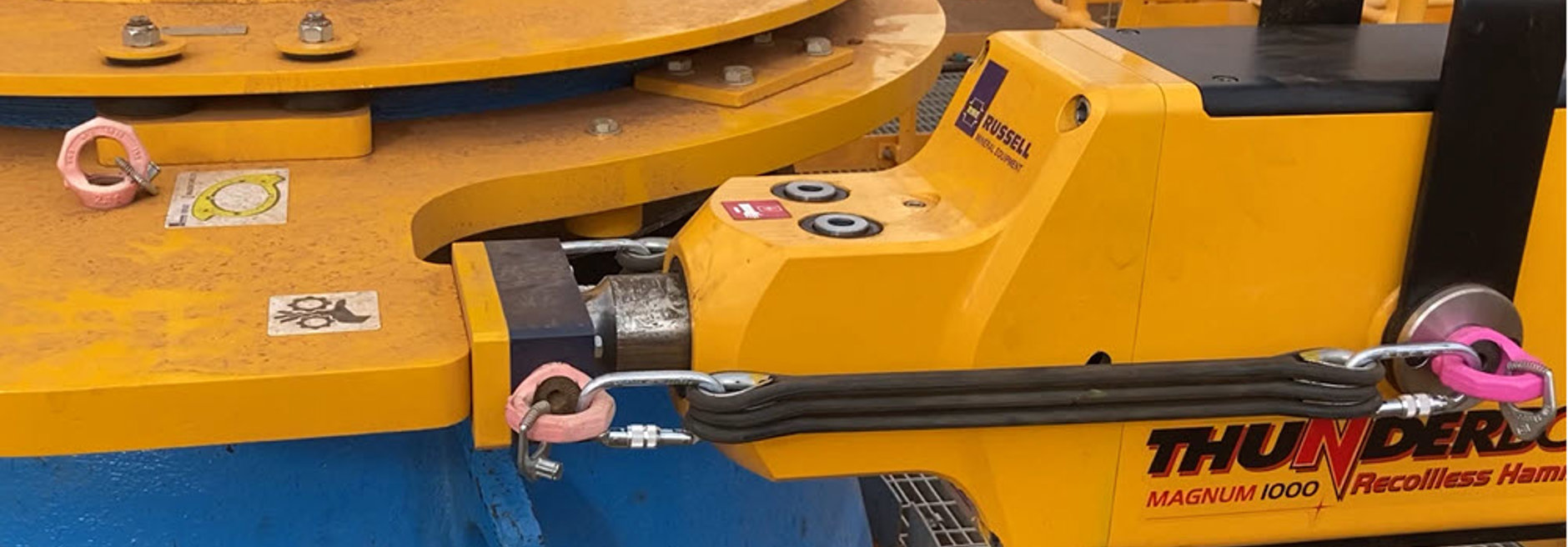
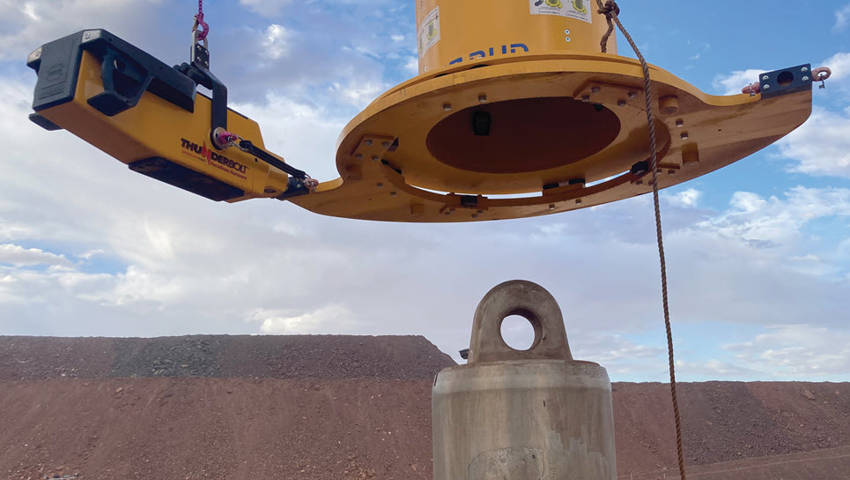
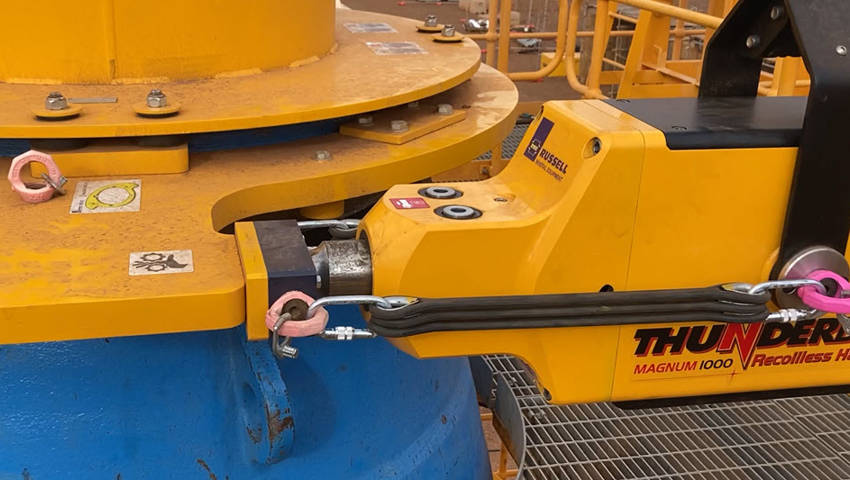
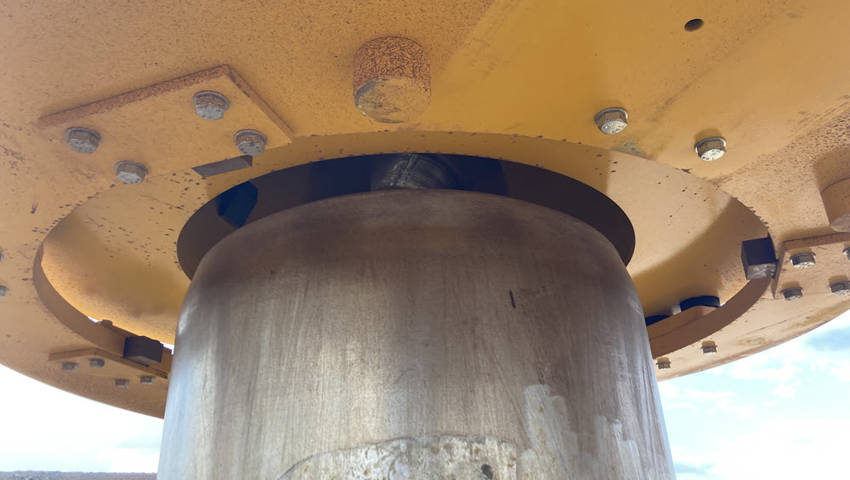
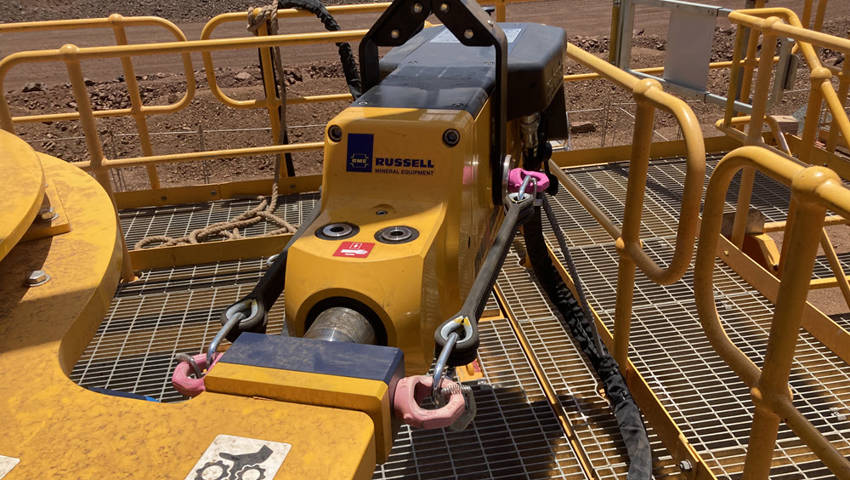
The THUNDERBOLT ORBIT™ is a revolutionary solution for gyratory and cone crusher head nut change outs. The system consists of a high-strength torque arm that receives consistent high-velocity blows from the THUNDERBOLT Recoilless Hammer, to deal with head nuts swiftly and easily. Most importantly, the ORBIT eliminates hazardous, time-consuming and physically demanding methods that rely on manual slugging, unfit-for-purpose tools and field welding. It represents the crusher industry’s fastest and safest method for mainshaft maintenance.
Benefits
- Reduces crusher downtime and improves reliability.
- Eliminates hazards, protects personnel, improves HSE compliance.
- Safeguards plant and equipment asset integrity.
- Expands THUNDERBOLT Recoilless Hammer utilisation.
- Optimises maintenance resources and costs.
- Frees up personnel for other critical-path tasks.
- Improves operational efficiency and safety.
- Higher crusher availability and throughput.
ADDITIONAL INFORMATION
-
- Integrated, all-in-one solution for gyratory and cone crusher head nut change-outs.
- High-strength torque arm ensures secure grip and even force distribution to all faces of the nut for significantly safer and faster loosening and tensioning.
- Lashing points for secure transport and crane lifting lugs as-standard for easy onsite portability.
- Purpose-built to work with the high-performance THUNDERBOLT Recoilless Hammer range – a proven technology with over 40 years of reliability in fast, safe grinding mill liner change-outs.
- 360-degrees suspension arm for optimal reach and easy THUNDERBOLT Hammer repositioning.
- Configurable counterweight balancers for different THUNDERBOLT Hammer models.
- Moil-locating socket for safe, optimised THUNDERBOLT Hammer firing alignment
- Share THUNDERBOLT Hammers across grinding mills and crushers for increased asset utilisation.
- Optional transport frame with forklift tyne pockets
-
- Custom-engineered and quality manufactured for precise fit and optimal performance for your crusher application.
- Site trials and commercial use have demonstrated significant reductions in gyratory and cone crusher head nut change-out time. For example, in one case, the average change-out time for a FIXED shaft crusher, was reduced from three to four (3-4) hours to around 15-20 minutes. For LIVE shaft crushers, change-out time was reduced from a full 12-hour shift to around one (1) hour.
- Available as an all-in-one solution. The ORBIT torque arm is also available as an add-on unit for existing THUNDERBOLT Recoilless Hammer users.
RME is the world’s leading Original Equipment Manufacturer (OEM) of mill relining systems.
RUSSELL MRMs engineered, manufactured and delivered.
THUNDERBOLT Recoiless Hammers sold.
Mine sites served by RME assets & services.
"The toughest maintenance tasks demand capable technologies that handle the conditions safely. The THUNDERBOLT ORBIT is a clever combination of the industry’s most powerful, proven and reliable THUNDERBOLT Recoilless Hammer and a purpose-built crusher head nut torqueing technology. It delivers a step-change to the way operations change-out crusher head nuts – with vastly improved speed and safety."
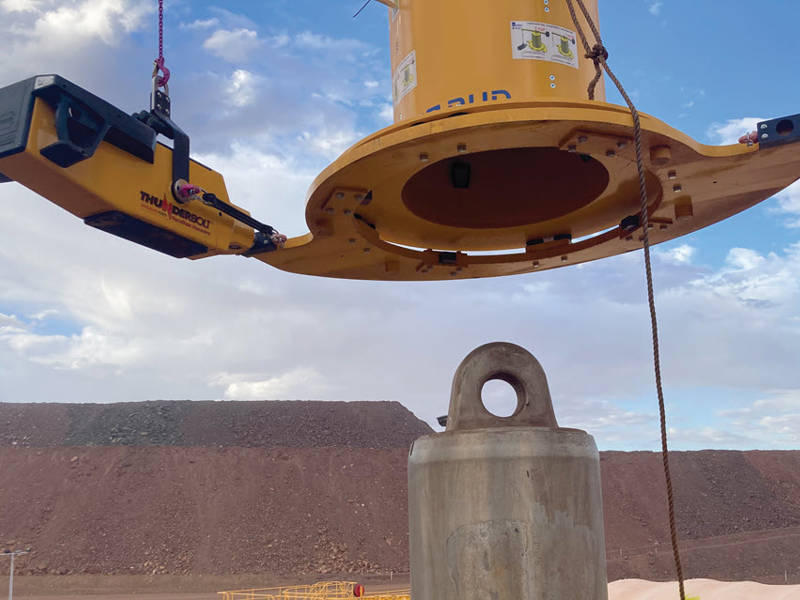
Compare THUNDERBOLT Recoilless Hammers
MODELO THUNDERBOLT |
MAGNUM 2000 |
MAGNUM 1000 |
1500 SP |
750 SP |
500 |
250 |
---|---|---|---|---|---|---|
ENERGÍA |
Hidráulica |
Hidráulica |
Hidráulica |
Hidráulica |
Neumática |
Neumática |
FUERZA GOLPE (J) |
2000 MM 1500 SM |
1000 MM 750 SM |
1500 |
750 |
500 |
250 |
Intervalo servicio |
100.000 golpes o 2 años |
100.000 golpes o 2 años |
40.000 golpes o anualmente |
40.000 golpes o anualmente |
40.000 golpes o anualmente |
Anualmente |
Tasa golpe (GPM) |
80 - Modo Estándar 70 - Modo MAGNUM |
160 - Modo Estándar 140 - Modo MAGNUM |
60 – Modo Estándar |
90 – Modo Estándar |
60 – Modo Estándar |
60 – Modo Estándar |
Related products
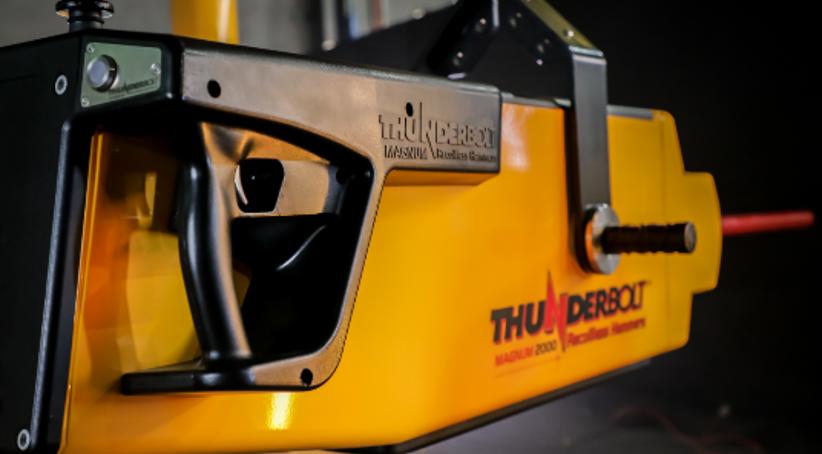
THUNDERBOLT MAGNUM 2000
The mighty THUNDERBOLT MAGNUM 2000 is the industry’s most powerful recoilless hammer, delivering the ultimate in impact energy per blow.
Read More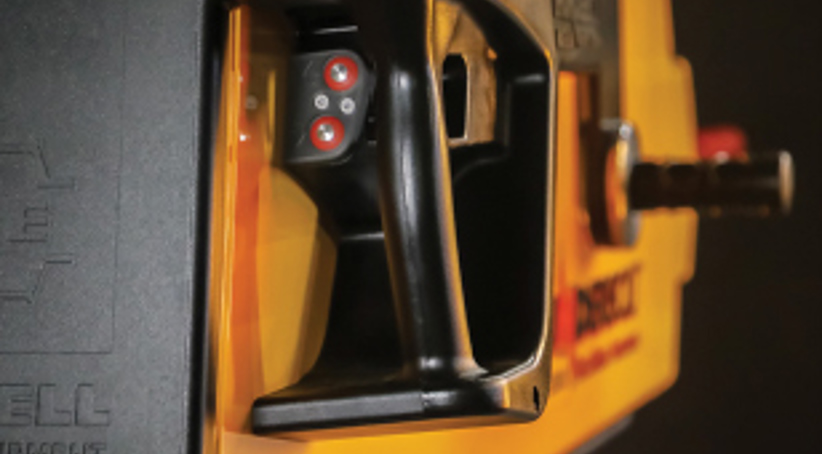
THUNDERBOLT MAGNUM 1000
The THUNDERBOLT MAGNUM 1000 is the industry's most productive hammer yet. It's high-energy rapid-fire rate will shorten knock-in times and improve operator safety.
Read More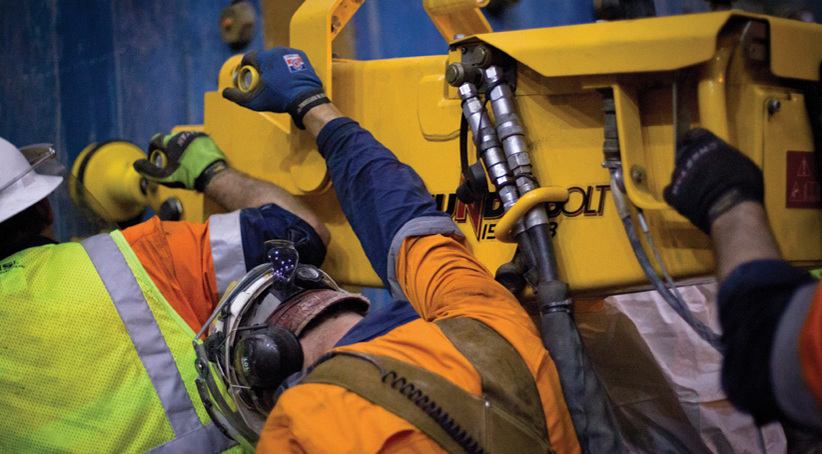
THUNDERBOLT 1500 SP
Favoured by mill operators and reline crews for its legendary reliability, the THUNDERBOLT 1500 SP is renowned for delivering powerful productivity and supreme operator safety.
Read More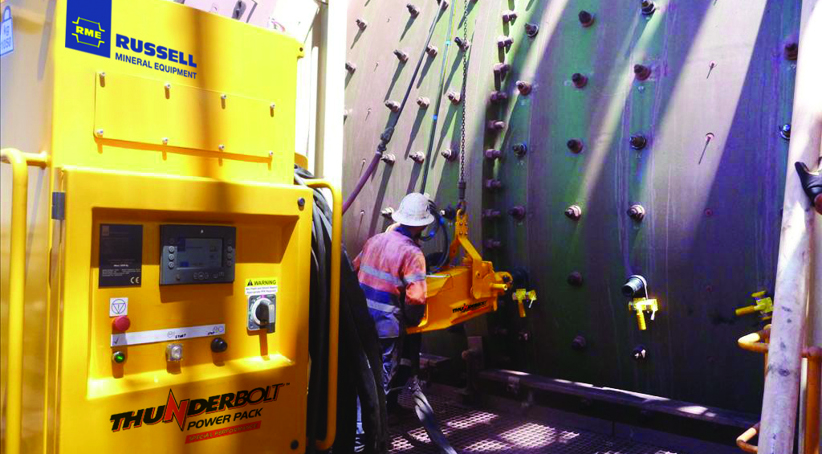
THUNDERBOLT 750 SP
A field favourite, the THUNDERBOLT 750 Special Performance Recoilless Hammer is highly regarded for its versatility, work-rate, responsive handling and RME reliability.
Read MoreOur Experts
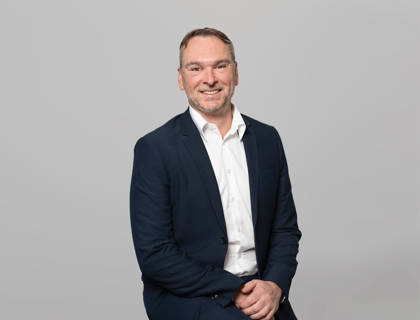
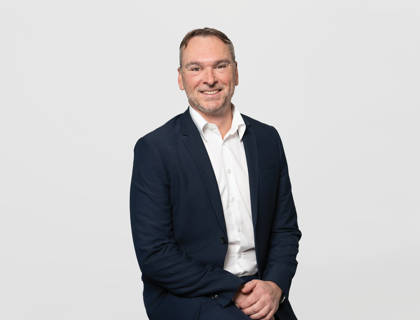
Tim Kruger
Service Account Manager, East Coast & South Australia
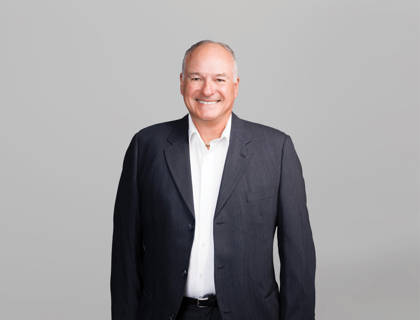
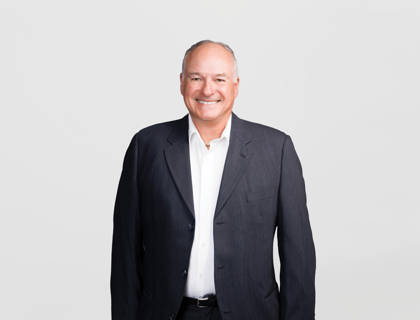