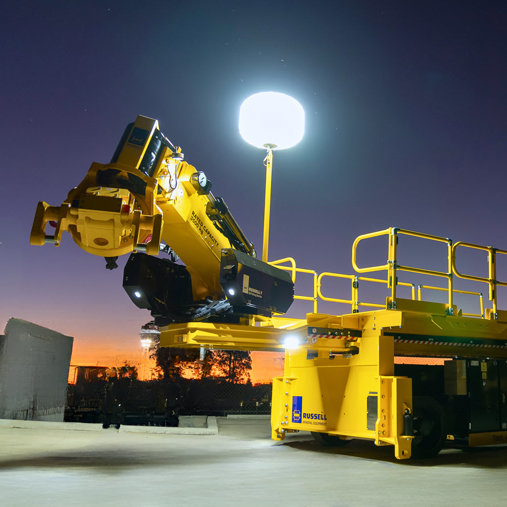
LINER EXCHANGE MACHINES
The preferred choice for mill operators globally. Our expanded range – 400 kg to 9T capacities – ensures fast, reliable, safe mill relining is now available to every site.
Trust RME to raise the standard
With 35+ years of innovation, we continually raise the standard of mill relining productivity and safety. Our technologies are built to last and deliver higher mill availability at lower total cost of ownership. We are RME.
Trust RME to raise the standard
Tough, durable and strong, the new RUSSELL Claw is the master of muck-out and eliminator of hazardous manual liner slinging. Lifting capacities up to 8000 kg.
Trust RME to raise the standard
Tap into trusted performance data, advanced technologies, training and coaching, and guide your operations to improved concentrator performance and mill relining safety – measurably, repeatedly, sustainably.
Trust RME to raise the standard
Well-maintained machines are safe machines. Leverage RME's global OEM experience, data-driven insights and practical ways to maximise asset reliability, compliance and longevity.
Trust RME to raise the standard
An innovative, productive safety technology that enables liner bolts to be secured from outside the mill during the liner placement phase of mill relining.
Since 1985, RME has been the global leading manufacturer and supplier of grinding mill relining technologies and optimisation services.
Mill relining is the most specialised and important task in the maintenance of a mineral concentrator. Mill relining dictates shut down times, mill availability and utilisation, through-put, and therefore mine site profitability.
RME’s passion and mission has always been to minimise mill relining time and to increase relining crews’ safety. RME Mill Relining System technologies, used effectively, have quartered the time taken to reline large minerals processing grinding mills. Looking forward, RME’s focus is to secure the potential of RME’s Mill Relining System performance for each and every one of our Customers, past, present and future.
Our commitment to industry is to visibly, defensibly and sustainably improve our Customers’ concentrator performance. Discover today how the RME Mill Relining System is delivering exceptional safety and performance for our Customers around the world.
The preferred choice for mill operators globally. Our expanded range – 400 kg to 9T capacities – ensures fast, reliable, safe mill relining is now available to every site.
Since 1997, THUNDERBOLTs have revolutionised liner bolt removal time and safety. See the wider range and their new faster, safer semi-automated capabilities.
Ensure mill relining equipment safety, productivity and longevity with RME's regionally-based inspections and servicing, critical spares provisioning and certified training.
Since the introduction of the RME Mill Relining System, we’ve quartered our Customers' traditional mill relining times. In addition, a great many safety issues associated with manual relining activities have been eliminated.
This same pursuit has driven our development of RME's Advanced Technology suite which removes the need for crew to be inside the mill during relining – an environment which enables us to significantly accelerate machine movements and relining speeds.
For more than 35 years, we’ve worked with hundreds of mine sites globally to optimise their mineral processing operations. Our mission is to work with you to create high production rates, short shutdowns and safe working environments.
RUSSELL MRMs manufactured since 1985
RUSSELL MRMs still in service and supported RME
THUNDERBOLT Recoilless Hammers manufactured
Mine sites / Countries with RME equipment
International Sales and Service Centres
Employees worldwide