22 April 2024
RME wins multiple awards at Australia’s 50 Most Innovative Manufacturers Event
RME is honoured to have been named the winner of Australia’s 50 Most Innovative Manufacturers Export Award and receive a Top Ten Gold Award at the Australian Manufacturing Forum event in Sydney on April 18, 2024
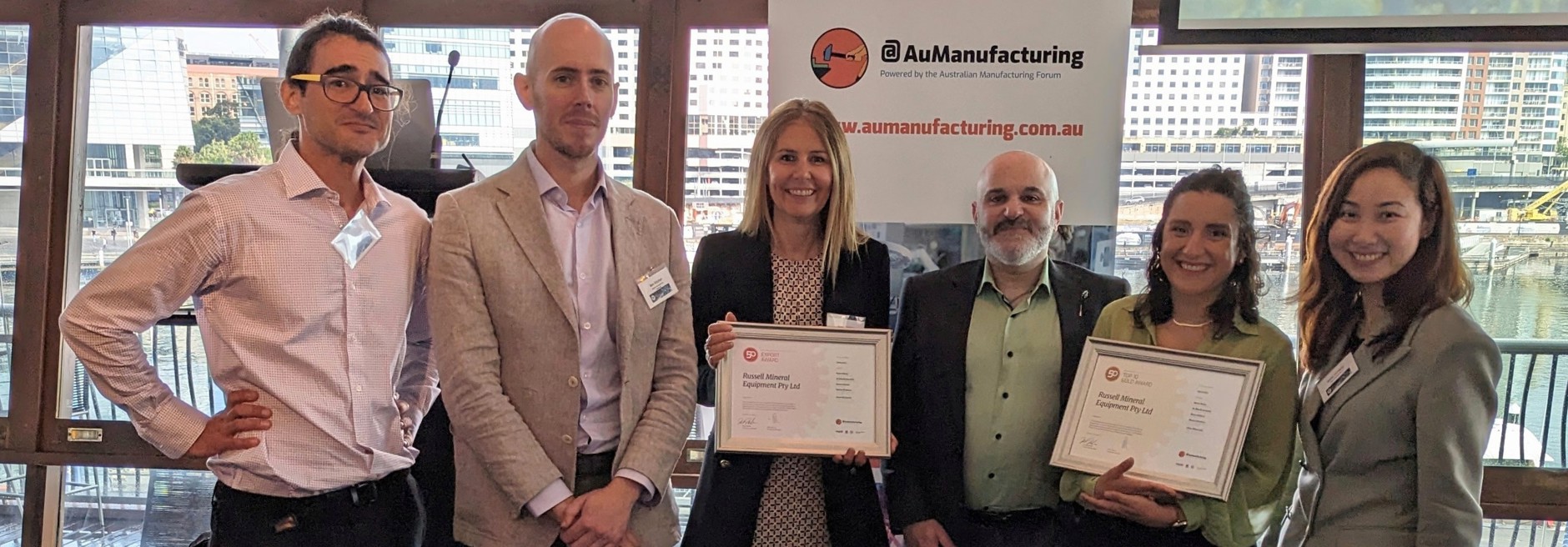
RUSSELL MINERAL EQUIPMENT (RME) is honoured to be named the winner of Australia’s 50 Most Innovative Manufacturers Export Award category and to receive a Top Ten Gold Award at the Australian Manufacturing Forum Event which was held in Sydney on April 18.
Australia’s 50 Most Innovative Manufacturers is an annual initiative by @AuManufacturing, supported by judges from MYOB, CSIRO, the NSW Government’s Advanced Manufacturing Research Facility, and the Commonwealth Bank of Australia. This program aims to recognise excellence in manufacturing across Australia.
"RME is thrilled to receive these two awards from @AuManufacturing," said Cherylyn Russell, Chief Customer Officer. "This recognition reflects our commitment, since our beginnings in 1985, to develop innovative solutions that improve the safety and productivity of grinding mill operations. We wholeheartedly thank the judges for acknowledging RME's dedication to the global mineral processing industry.
“We also congratulate all the worthy award winners. Hearing the innovation journeys of fellow Australian OEMs across a range of diverse sectors underscored a powerful truth: innovation thrives not just in ideas, but also in the doing."
RME is the world’s leading original equipment manufacturer (OEM) and supplier of grinding mill relining technologies and optimisation services for hard rock mineral concentrators.
Replacing worn liners in mineral concentrators is widely acknowledged as one of the most hazardous surface jobs at a mine site, with risks comparable to underground mining. Crews often work in hot, dark, confined spaces, handling multi-ton suspended loads, and in proximity to heavy mobile plant and equipment.
Prior to the delivery of the first RUSSELL Mill Relining Machine in 1990, this necessary maintenance process relied heavily on manual handling, which posed significant safety risks to workers. Furthermore, each mill shutdown for relining meant lost production hours and a substantial financial cost.
In the three plus decades since, RME has collaborated with Customers to identify areas where innovative engineering solutions can deliver economic and safety benefits. These efforts culminated in the development of the ‘RME Mill Relining System’ – a suite of technologies that has revolutionised grinding mill relining globally.
The industry impact of RME’s engineering innovation has been evident from the outset. The production of the first mechanised RUSSELL Mill Relining Machines (MRMs) revolutionised liner manipulation, enabling the casting of progressively larger liners and reducing the number of pieces requiring change-out, and so too the time taken to complete relining.
This advancement also facilitated the development of larger semi-autogenous grinding (SAG) mills, tailored to accommodate the largest available RUSSELL MRMs at the time. RME still boasts the world’s highest capacity machine, capable of handling liners up to an impressive 10 tonnes.
RME's General Manager of Manufacturing, Geoff Wadsworth, described the RUSSELL MRM as an engineering and manufacturing marvel that incorporates a range of mechanical, hydraulic, electrical, electronic, and robotic software systems.
"Imagine a large cantilever crane that is subject to regular shock loads, yet positions heavy-weight liners at unconventional angles with millimetre precision.
“We custom-engineer each machine to meet the exact specifications, like mill size, feed diameter, and liner type and weight, of its designated SAG, AG, or ball mill application.
“Our lean manufacturing processes have allowed us to deliver a custom machine every seven working days at our facilities in Toowoomba, a feat we consistently achieved during the peak of the mining boom."
“Furthermore, our products boast unrivalled quality, reliability and longevity, enduring even the most demanding mine site environments.
“They are a true testament to RME's exceptionally robust engineering and lean practices in manufacturing, fabrication, and assembly."
In September 2023, RME announced another significant industry milestone with the successful commercial deployment of the world’s first roboticised mill relining system – the ‘RME Advanced Technology Mill Relining System’. This ground-breaking capability enables mill operators to reline concentrators without the need for personnel to enter the hazardous confines of the mill.
Reflecting on the significance of these achievements, Dr. John Russell, RME's Founder and Chief Engineer, stated, "RME, a proud Australian OEM, is at the forefront of developing innovative technologies for safer and more efficient mill relining for mineral concentrators worldwide.
"Our focus on innovation is more important than ever for our Customers, the majority of whom are copper producers. This focus is because the transition to net-zero will be heavily minerals-intensive.
“Our focus on innovation is more important than ever for our Customers, the majority of whom are copper producers. This is because the transition to net-zero will be heavily minerals-intensive."
“The Global Copper Alliance confirms this, revealing that the shift to cleaner forms of energy and transportation necessitates four to six times more copper than fossil fuel systems.
“This presents a global challenge that requires substantial scale-up in mineral extraction, processing, and innovative engineering solutions, all conducted with a keen eye on economic viability, environmental sustainability, and occupational safety.
We are proud of RME's role within this narrative."
RME’s proprietary technologies are deployed in over 440 mine sites worldwide. Furthermore, around 85% of RME’s revenue is from export earnings – something John Russell says is also a great source of pride for employees.
RME’s headquarters and global manufacturing operations continue to operate from Toowoomba, Queensland, Australia with 12 international sales and service centres in all major markets.
About RUSSELL MINERAL EQUIPMENT
RUSSELL MINERAL EQUIPMENT (RME) is the world’s leading Mill Relining Systems Technology supplier. We invent machine systems and service-based solutions for problems encountered in the world’s mining and mineral processing industries. Our technologies deliver short shutdowns, high mill availability and safe working environments. Established in 1985, RME has grown to operate in 64 countries, has 12 international Sales and Service Centres and employs more than 450 people worldwide.
For more information about RME: www.rmeglobal.com