01 November 2021
'The knock-in effect' of THUNDERBOLT MAGNUM Recoilless Hammers
Quantifying the impact of THUNDERBOLT MAGNUM Recoilless Hammer technology on reline duration and mill availability.
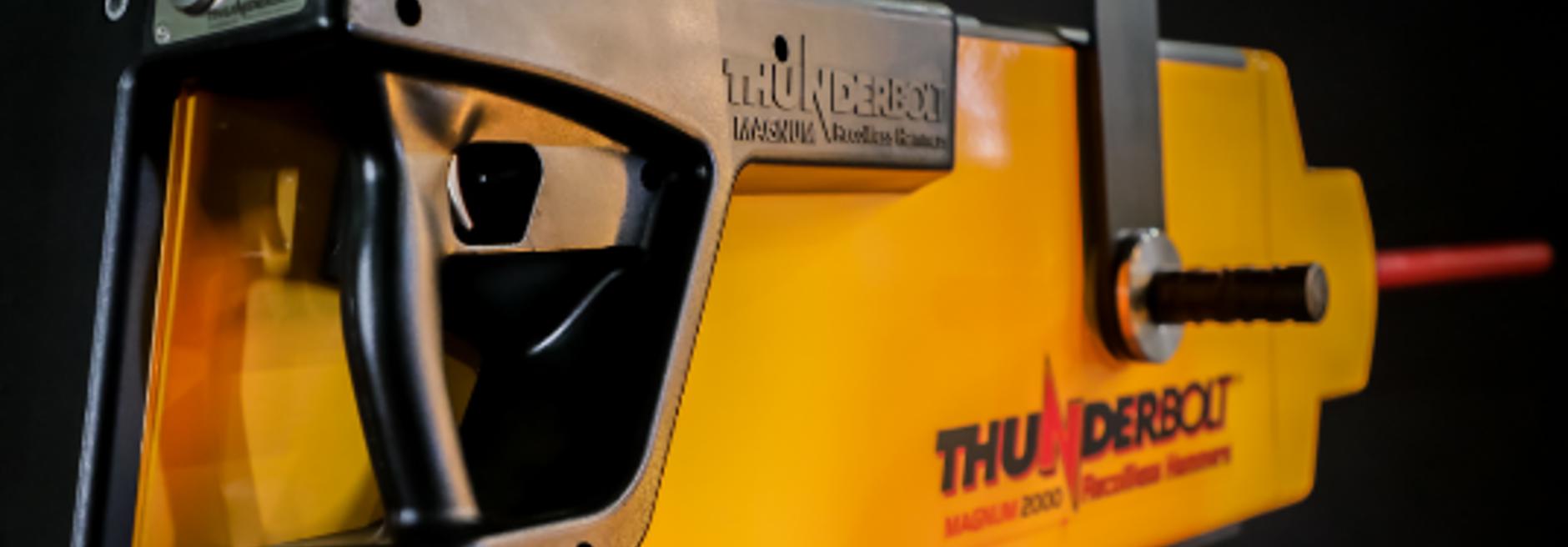
Grinding mill relining remains a major source of downtime in mineral processing plants. Optimisation of the relining process through correct equipment selection has been proven to increase plant throughput. At many sites, the mill reline is the critical path maintenance activity that has the single greatest impact on mill availability. Additionally, as one of the most hazardous maintenance activities in the processing plant, correct relining equipment selection also assists with managing the safety risks.
“The Knock-in Effect” whitepaper shares the results of a study undertaken by RME Engineers which investigated the impact of the latest-generation THUNDERBOLT MAGNUM Recoilless Hammers’ increased strike energy and firing rate on the worn liner knock-in phase.
THUNDERBOLT Recoilless Hammers replace sledgehammers and battering rams for the liner and bolt knock-in process, which typically represents between 20-30% of relining downtime. The new THUNDERBOLT MAGNUMs provide mine sites with greater strike impact, speed, serviceability and operator safety than previous models.
RME conducted the investigation using the company’s proprietary discrete event simulation tool called MILL RELINE DIRECTOR (MRD). It essentially created a ‘digital twin’ of a mill relining event based on time and motion studies. RME has also used physical testing in controlled environments as well as thousands of hours of filmed real world relines to calibrate and validate the results.
A key finding from “The Knock-in Effect” study was that optimal hammer configuration includes at least one THUNDERBOLT MAGNUM 2000 Recoilless Hammer. This is to assist with ‘breaking-in’ tough liners, such as those that have suffered heavy peening, or stuck bolts at the discharge-end of the mill. Additionally, multiple THUNDERBOLT MAGNUM 1000 Recoilless Hammers, which fire faster and are easier to maneuver, are highly advantageous for the remainder of the liners and liner bolts.
The results of the MRD study showed that when relines are more difficult, such as having more stuck bolts or peened liners requiring oxy-lancing, the introduction of the right complement of THUNDERBOLT MAGNUMs can increase annual mill availability by up to 0.5%, or 44.2 hours, for a large SAG mill, and 0.33%, or 28.5 hours for a medium SAG mill.
The results also found that when plant layouts are designed for good access on both sides of the mill, an optimal configuration of THUNDERBOLT MAGNUMs can create an additional 0.35%, or 30.6 hours, in annual mill availability compared to single sided relining for large mills, and 0.16%, or 14.7 hours, for medium mills.
Learn more about these results, and more, in the “The Knock-in Effect” whitepaper.
Register via the link below to secure your free copy.
Gain exclusive access to our THUNDERBOLT MAGNUM Recoilless Hammer engineering performance whitepaper
“Achieving continual improvements in mill relining speed and safety is how RME delivers value and competitive advantage. Being able to use MILL RELINE DIRECTOR's scientifically-defensible methodology to quantify return on technology investment helps Customers make informed decisions and reduce CAPEX risk. This is a strong reason to partner with RME.”