THUNDERBOLT ELEVATING PLATFORMS
Give your crews greater, and ergonomically-safer, reach outside the mill. Plus they're field-upgradable to THUNDERBOLT SKYPORT.
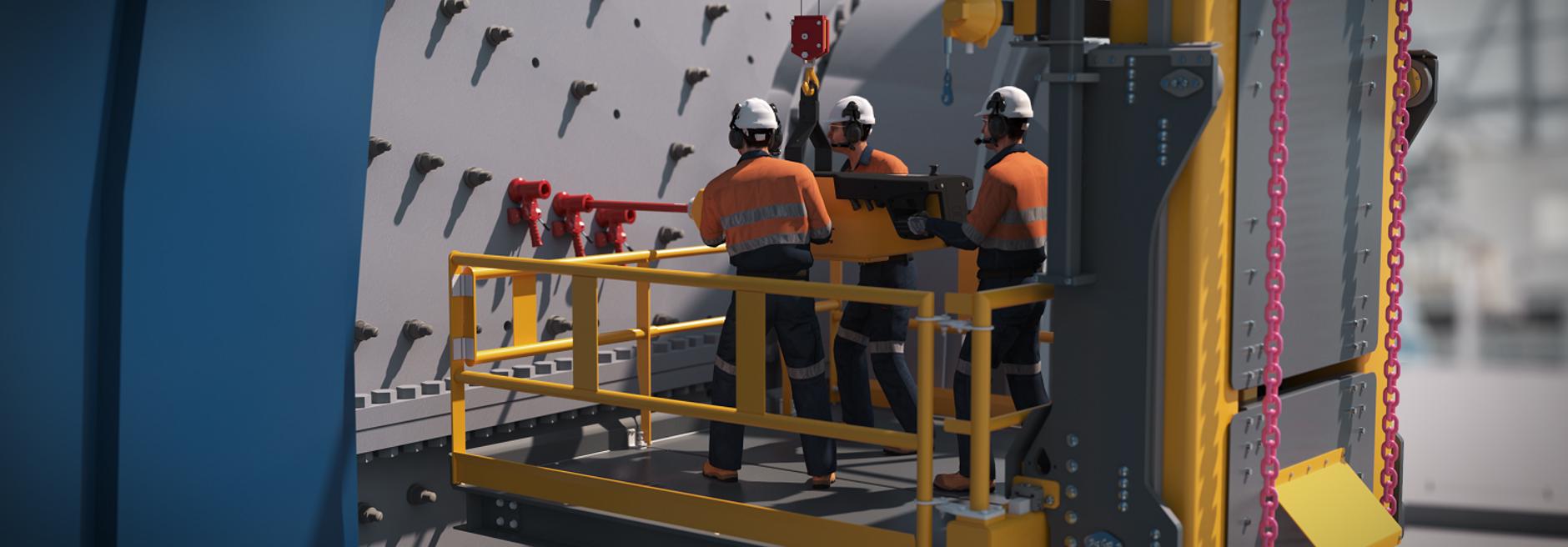
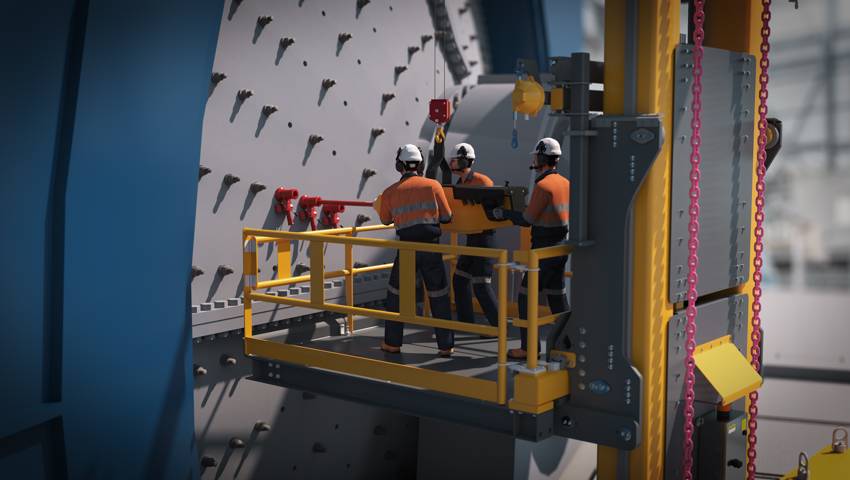
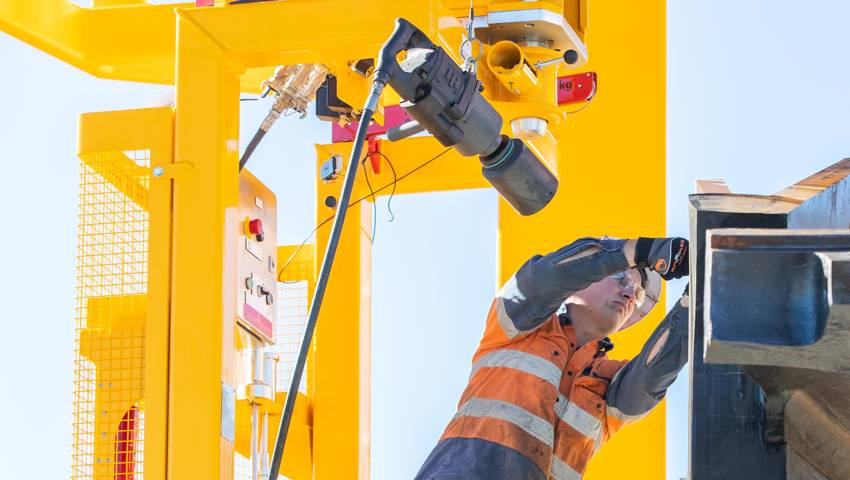
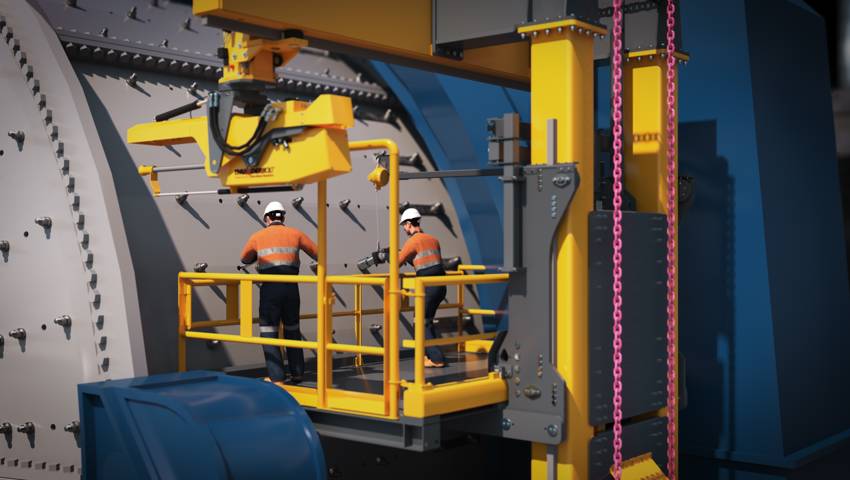
Portable, modular, safer – THUNDERBOLT ELEVATING Platforms help mine sites reduce risk and reline time during worn liner removal and activities outside the mill.
THUNDERBOLT ELEVATING Platforms provide reline crews with greater and reach for faster nut removal and liner knock-in. Most importantly it provides an ergonomically safer means of doing so.
Advance processes even further with an easy upgrade to SKYPORT’s semi-automated precision guidance of THUNDERBOLT Recoilless Hammers – the ultimate in hazard elimination and reline speed.
BENEFITS
- Portable modular solution which integrates jib suspension and elevating work platforms
- Crane lift-in and sharable between mills
- Provides greater mill reach and an ergonomically safer way to work outside of the mill
- Improves safety, reduces worker fatigue and risk of injuries, especially at high-altitude sites
- Offers access to up to 6 rows of liner bolts, 2x to 3x more than traditional methods
- Reduces time-consuming mill inching cycles requirements
- Improves mill relining productivity, leading to greater mill availability
- Field-upgradable to THUNDERBOLT SKYPORT for remote automated hammer control
- Complements RME INSIDEOUT Technology
- Utilises proven technology deployed in concentrator plants globally
- Backed by RME 24/7 SERVICE and over 35 years of trusted OEM expertise
ADDITIONAL INFORMATION
-
- Reach more bolt rows without mill inching – Access up to 6 liner bolts rows which is 2x to 3x higher than humans can safely reach.
- Ergonomic elevating operator platform – 10-person capacity for shell configurations and 5-person for feed and discharge configurations.
- Deploy as a safer work platform – Add booms for air tools, and right or left telescoping jibs for hammer suspension.
- Integrated suspension – Multiple universal jib mounts for hammer suspension.
- Works with existing site equipment – THUNDERBOLT MAGNUM Recoilless Hammers, Power packs and THUNDERBOLT Jibs.
- Crane-transportable – Easy connection to overhead crane makes for one simple lift to remove from side of mill to offline service area.
- Portable across multiple mills – Increases asset utilisation and returns on asset usage.
- Reliable hydraulic operation – All components are tested and quality certified for harsh site conditions.
- Automation upgradeability in-the-field – Easy upgrade path to automated high-speed precision-guidance THUNDERBOLT SKYPORT knock-in technology.
- Collapsible guard rails – For safe working at-height with in-floor anchors for a fall arrest system when rails are folded.
-
- Ideal for mine sites with medium to large SAG, AG and ball mills or long-life mines seeking to achieve sustainable step-change improvements in risk, safety and mill availability.
RME is the world’s leading Original Equipment Manufacturer (OEM) of mill relining systems.
RUSSELL MRMs engineered, manufactured and delivered.
THUNDERBOLT Recoiless Hammers sold.
Mine sites served by RME equipment & services.
“THUNDERBOLT ELEVATING Platforms are an innovative portable and modular solution. They integrate THUNDERBOLT Hammer jib suspension and work platforms for greater mill reach and an ergonomically safer way to work outside of the mill. Best of all they can be upgraded in the field to THUNDERBOLT SKYPORT for automated high-speed precision hammer guidance and bolt knock-in.”
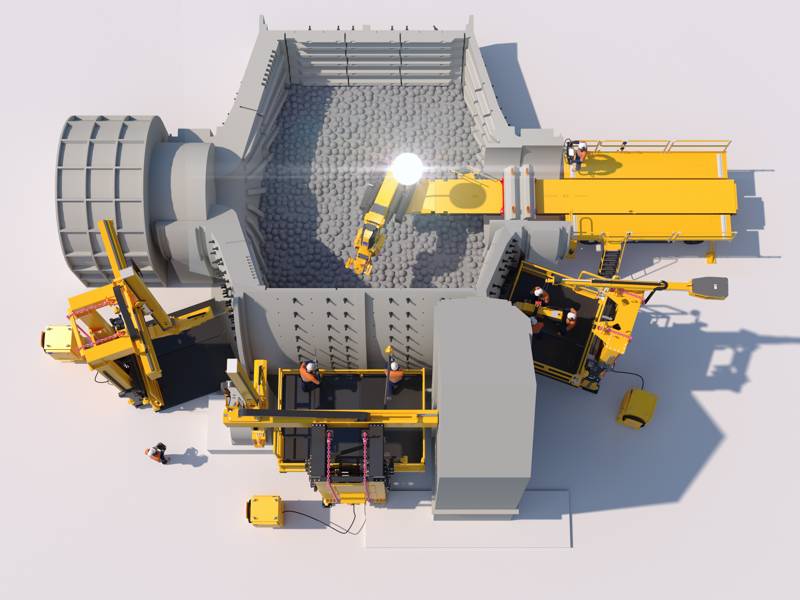
Choose your advanced knock-in solution
Benefits |
THUNDERBOLT Elevating Platforms |
THUNDERBOLT SKYPORT |
THUNDERBOLT SKYWAY |
---|---|---|---|
Portability between mills |
Crane portable |
Crane portable |
Fixed |
Mill size |
24 ft and up |
28 ft and up |
36 ft and up |
THUNDERBOLT integration |
Hammer / Power Pack / Jibs |
Hammer / Power Pack |
Hammer / Power Pack |
THUNDERBOLT automation |
No. Guided suspension |
Semi-automated |
Semi-automated |
Work platform operable when hammer in use |
Yes |
No. Due to autonomous hammer modules. |
Yes. Work platforms are independent of autonomous hammer modules. |
Integrated arm for tool suspension |
Optional |
Optional |
Standard |
Liner bolt reach |
Up to 6 rows |
Up to 6 rows |
Up to 6 rows |
Suitable for gearless mill drive (GMD) servicing |
Yes |
Yes |
Yes |
Plant installation method |
Anchor points |
Anchor points |
Fixed foundations |
Electrical safety interlocks |
On handrails |
On handrails |
On work platform modules |
Safety uplift |
Ergonomically safer worn liner bolt removal and new liner bolt securing. |
Semi-automated hammer operation removes crew from hazardous zones. |
Semi-automated hammer operation removes crew from hazardous zones and enables safe concurrent crew and knock-in operations. |
Related products
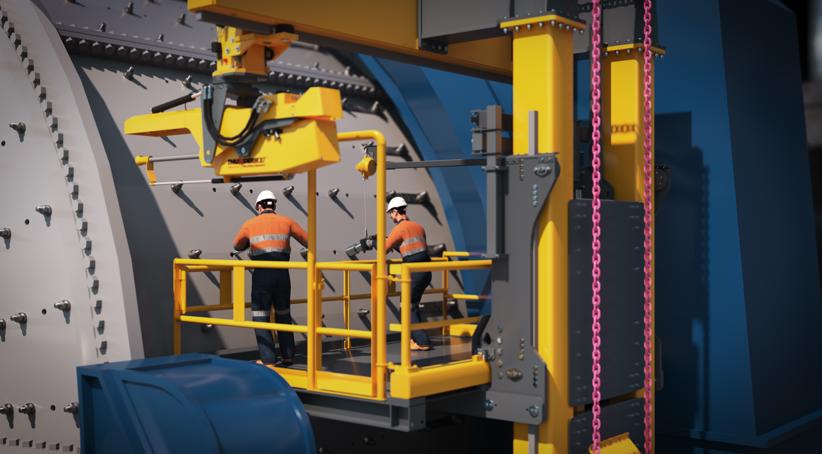
THUNDERBOLT SKYPORT
Portable and modular, THUNDERBOLT SKYPORT is the lift-in version of the fixed plant THUNDERBOLT SKYWAY, RME's semi-automated knock-in technology.
Read more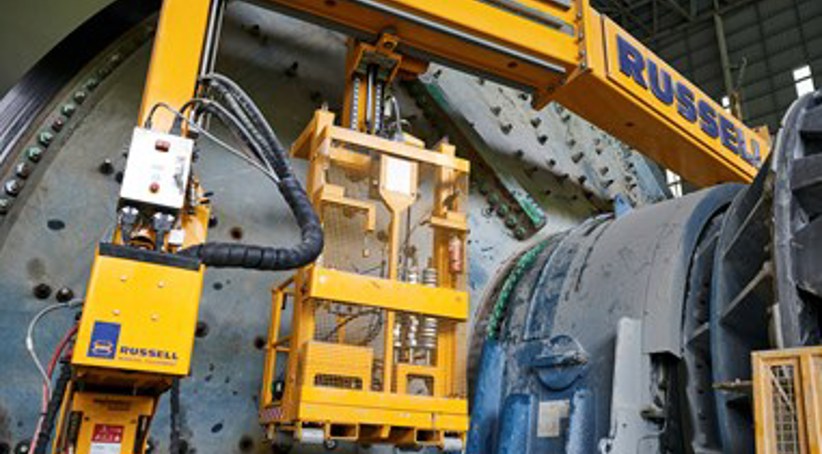
THUNDERBOLT SKYWAY
THUNDERBOLT SKYWAY roboticises the operation of THUNDERBOLT Hammers to vastly improve knock-in speed and safety – consistently, repeatably, sustainably.
Read more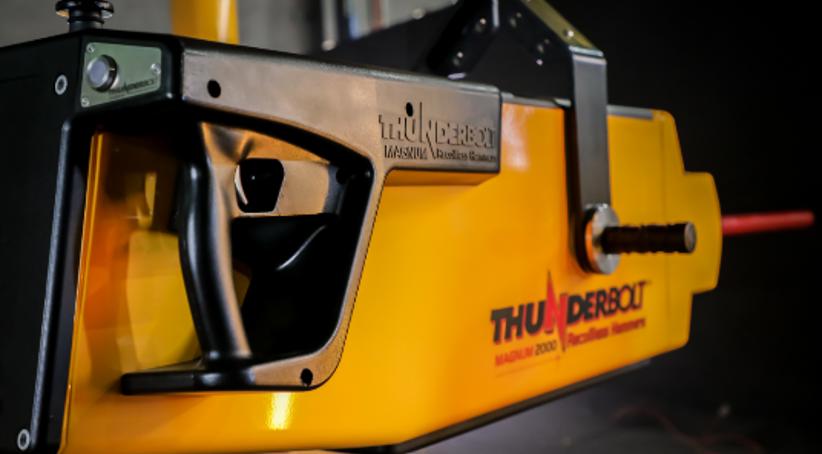
THUNDERBOLT MAGNUM 2000
The mighty THUNDERBOLT MAGNUM 2000 is the industry’s most powerful recoilless hammer, delivering the ultimate in impact energy per blow.
Read more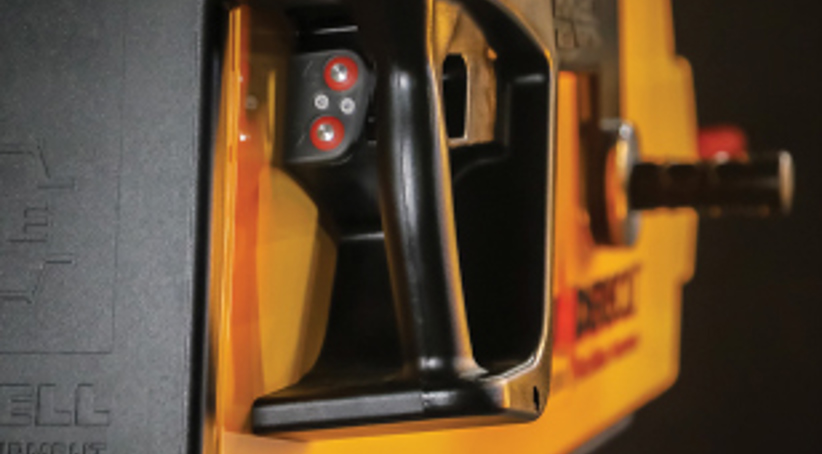
THUNDERBOLT MAGNUM 1000
The THUNDERBOLT MAGNUM 1000 is the industry's most productive hammer yet. It's high-energy rapid-fire rate will shorten knock-in times and improve operator safety.
Read moreOur Experts
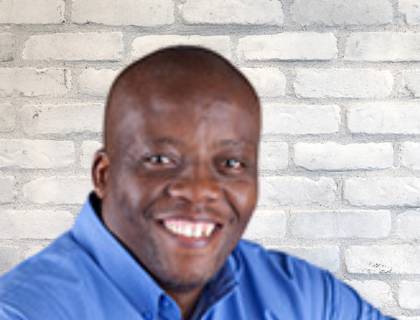
Kabelo Mogobye
Regional General Manager - Africa
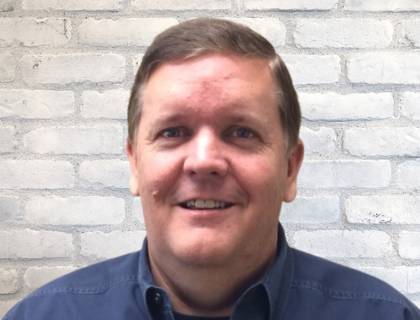
Denny Wisely
Vice President Sales & Business Development - North America
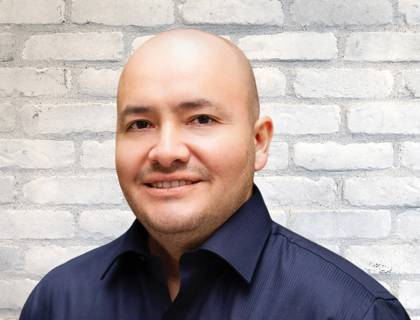